Author:Date:2025-5-2
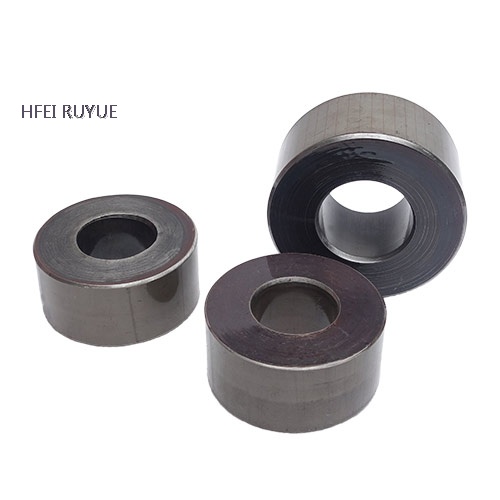
Wound cores are commonly used in small and medium-sized transformers (below 1000 kVA), transformers, magnetic amplifiers, and zero-sequence current transformers for leakage protection devices, etc. The materials used for wound cores are high-permeability ultra-thin cold-rolled silicon steel sheets and permalloy and other soft magnetic tapes. The thickness of silicon steel sheets is 0.18 to 0.30 mm; the thickness of permalloy tapes is 0.03 to 0.10 mm. Taking small and medium-sized transformers as an example, the advantages of using wound cores are as follows:
1. Under the same conditions, compared with laminated cores, the no-load loss of wound cores can be reduced by 7% to 10%, and the no-load current can be reduced by 50% to 75%.
2. Wound cores can use very thin high-permeability cold-rolled silicon steel sheets, which can produce transformers with lower losses.
3. Wound cores have good processability, no cutting waste, and the utilization rate is almost 100%. They can also be produced by mechanized operations, eliminating the lamination process, and the production efficiency is 5 to 10 times higher than that of laminated cores.
4. Wound cores are an integral whole and do not require support pieces for clamping and fixing, and there is no seam. Therefore, under the same conditions as laminated cores, the noise of the transformer can be reduced by 5 to 10 dB.
5. The process coefficient of wound cores is about 1.1 for single-phase transformers and less than 1.15 for three-phase transformers. For laminated cores, the process coefficient is about 1.45 for small-capacity transformers and about 1.15 for large-capacity transformers. Therefore, wound cores are particularly suitable for small and medium-sized transformers.
Comparison of three-dimensional triangular wound cores, laminated cores and planar wound cores
1. Three-dimensional triangular wound core
Three-dimensional wound core: A core formed by assembling three single frames of wound cores with the same geometric dimensions in a triangular three-dimensional arrangement.
Three-dimensional wound core transformer: A distribution transformer with a three-dimensional wound core as its magnetic circuit.
Process features: The entire core is composed of three identical single frames. After assembly, the three core columns of the core form an equilateral triangular three-dimensional arrangement. Each single frame is formed by continuously winding several trapezoidal material strips in sequence. The cross-section of the wound single frame is close to a semicircle, and the cross-section after assembly is a quasi-polygon very close to a full circle. The trapezoidal material strips of different sizes for winding the single frames are obtained through nesting processing by a dedicated zigzag cutting machine. This nesting processing can achieve zero waste processing, that is, the material utilization rate during nesting is 100%.
2. Laminated core
Laminated core: It is formed by processing silicon steel strips into silicon steel sheets of a certain shape through longitudinal and transverse cutting lines, and then stacking the silicon steel sheets in a certain way.
The laminated core has three disadvantages:
There are many air gaps formed by joints in the magnetic circuit, which increase the magnetic resistance of the magnetic circuit, thereby increasing losses and no-load current.
The direction of the magnetic circuit in some local areas is inconsistent with the high magnetic permeability direction of the silicon steel strip.
The sheets are not tightly stacked, which not only reduces the stacking factor but also increases noise.
The influence of the process on losses
Longitudinal and transverse cutting generate mechanical stress, increasing losses
The magnetic circuit direction at the corners is inconsistent with the magnetic permeability direction, resulting in high magnetic resistance and increased losses
Joints increase losses, especially no-load current
The process coefficient is 1.15 to 1.3
The influence of the structure on the magnetic circuit
In the traditional laminated core with air gaps, the coupling magnetic circuit between phases A and C is obviously 1/2 longer than the magnetic circuits between phases A and B and B and C, resulting in an unbalanced magnetic circuit. The magnetic resistance of the magnetic circuit between phases A and C is relatively large. When three-phase voltage is applied to the transformer, the core generates three-phase balanced magnetic fluxes φA, φB, and φC.
When the three-phase balanced magnetic fluxes pass through the unbalanced magnetic circuit, the magnetic pressure drop between phases A and C is large, affecting the balance of the three-phase voltage. This imbalance in the magnetic circuit is an unovercome structural defect for planar transformers.
3. Planar wound core
Planar wound core: A core formed by combining one or more single frames of wound cores in a planar arrangement.
Process features: The planar wound core is formed by first winding two smaller inner frames, and then combining them and winding a larger outer frame on the outside. The three core columns of the planar wound core are arranged in a planar manner. Structural disadvantages of the planar wound core
Like the laminated core, the three core columns of the planar wound core are arranged in a planar manner, which makes the magnetic circuit lengths of the three core columns inconsistent: the magnetic circuit length of the middle column is short, while the magnetic circuit lengths of the two side columns are longer, with an average magnetic circuit length difference of about 20%. This results in significant differences in no-load losses among the three core columns: the no-load loss of the middle column is low, while the no-load losses of the two side columns are relatively high, causing three-phase imbalance.